|
Home >
Business
>
Business
>
Re-manufactured Motors Save Resources and Energy
Re-manufactured Motors Save Resources and Energy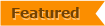
Electric motors make it possible for modern industry to survive and thrive. They don't get much attention or thought, but everything from a small home appliance to heavy industrial water treatment facilities use electric motors.
Caldwell,
ID,
United States
(pr4links.com)
07/01/2013
Electric motors make it possible for modern industry to survive and thrive. They don't get much attention or thought, but everything from a small home appliance to heavy industrial water treatment facilities use electric motors. In fact, according to some well known studies, electric motors account for over 40% of global electricity usage.
It is for that reason that many organizations are paying close attention to ways to make electric motors more efficient. One way that is gaining more and more popularity is by using re-manufactured electric motors. Not only does the re-manufacturing process save natural resources, but in many cases, the electric motors end up being more energy efficient that new motors!
A repair or re-manufacture can be more efficient than the original fixture and that is mainly due to the fact that the re-manufacturing process requires attention to guidelines, details and specs that new motors are not. Electric motors and pumps are usually manufactured by on fast paced assembly lines, which do their job well, but the re manufacturing processes requires a hands on approach by trained professionals.
In order to make sure that repair work is always top notch, EASA (Electrical Apparatus Service Association) provides some some very strict rules and requirements. Experts analyze every part of the equipment and follow up with tests done by specialized machinery. Using state of the art test equipment is a very important part of doing a qualitative repair.
A professional repair team also looks into the history of the machinery, the way it was installed and the conditions in which it functioned in the last years. This information can tell them a lot about the cause of the problem and allows them to make suggestions and changes on how to make the motor more efficient and run longer.
Once a motor is brought to an authorized re-manufacturing facility, the motor is tested in several different ways.
1. The winding will be tested, vibration base lines measured, and if the motor wont run at all it goes to a complete dissasembly.
2. Parts are cleaned and inspected for electrical or mechanical damage.
3. The motor is hydro-cleaned, baked dry then dipped and baked in a special varnish made to withstand high temperatures.
4. Shaft bearings are measured to exact tolerances and repaired if necessary.
5. Shafts are checked for straightness, keyway condition, and size.
6. The rotor will then be dynamically balanced to perfection.
7. Bearings are completely replaced with high precision specialty bearings.
8. Then the motor is be reassembled, painted and tested to prove proper operation
All final tests are recorded and provided to the customer. Re manufacturing electric motors is probably not the first thing that comes to mind when thinking of ways to "go green" and save energy, however, the advantages are easy to recognize.
- Re manufacturing costs less than buying new.
- Valuable metals and resources are recycled
- Tolerances and efficiency are better than new in many cases.
- Warranties and Guarantees are offered Government grants and bonus are offered to qualifying businesses.
Saving energy should be a priority for every small or large application. If you are in need of a new electric motor, check first to see if your local provider has a re-manufactured motor program.
###
About
Started over 50 years ago, Priest Electric is a Boise based electric motor repair company. They also operate in Idaho, Nevada, and Oregon. To know more, visit, http://www.priestelectric.com/
|